The Best Strategy To Use For Alcast Company
The Best Strategy To Use For Alcast Company
Blog Article
The Best Guide To Alcast Company
Table of ContentsThe Best Guide To Alcast CompanyAlcast Company Things To Know Before You Buy3 Easy Facts About Alcast Company ShownThe Definitive Guide for Alcast CompanyFacts About Alcast Company UncoveredAn Unbiased View of Alcast Company
The refined difference depends on the chemical material. Chemical Contrast of Cast Aluminum Alloys Silicon promotes castability by lowering the alloy's melting temperature and boosting fluidity throughout casting. It plays a critical role in enabling intricate molds to be filled up precisely. In addition, silicon adds to the alloy's strength and wear resistance, making it important in applications where longevity is important, such as auto components and engine parts.It additionally enhances the machinability of the alloy, making it easier to process into completed products. This way, iron adds to the overall workability of light weight aluminum alloys. Copper raises electric conductivity, making it beneficial in electric applications. It additionally improves deterioration resistance and adds to the alloy's overall toughness.
Manganese adds to the toughness of aluminum alloys and improves workability. Magnesium is a lightweight element that supplies toughness and effect resistance to light weight aluminum alloys.
9 Easy Facts About Alcast Company Shown
Zinc improves the castability of aluminum alloys and helps control the solidification procedure during casting. It enhances the alloy's strength and firmness.
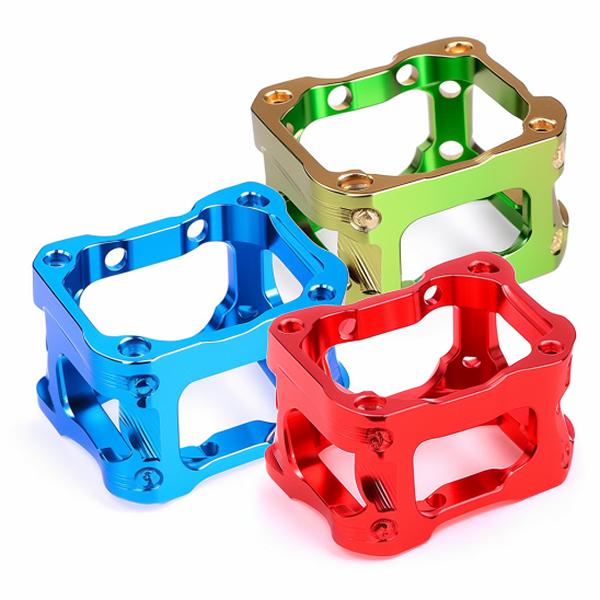
The primary thermal conductivity, tensile strength, return strength, and elongation vary. Among the above alloys, A356 has the highest possible thermal conductivity, and A380 and ADC12 have the least expensive.
How Alcast Company can Save You Time, Stress, and Money.

In accuracy casting, 6063 is fit for applications where elaborate geometries and high-quality surface area coatings are vital. Instances include telecommunication units, where the alloy's superior formability enables streamlined and visually pleasing styles while keeping structural stability. In a similar way, in the Lighting Solutions market, precision-cast 6063 parts develop elegant and effective lights fixtures that require elaborate forms and excellent thermal performance.
The A360 displays remarkable prolongation, making it ideal for facility and thin-walled parts. In accuracy casting applications, A360 is well-suited for sectors such as Customer Electronics, Telecommunication, and Power Tools.
The 30-Second Trick For Alcast Company
Its unique residential or commercial properties make A360 a beneficial option for accuracy casting in these markets, boosting product longevity and high quality. Light weight aluminum alloy 380, or A380, is a widely utilized spreading alloy with numerous distinctive attributes. It supplies outstanding castability, making it an excellent choice for accuracy spreading. A380 shows good fluidity when molten, ensuring elaborate and comprehensive mold and mildews are accurately replicated.
In accuracy casting, light weight aluminum 413 radiates in the Consumer Electronic Devices and Power Equipment industries. This alloy's premium rust resistance makes it an outstanding choice for exterior applications, making sure lasting, durable items in the discussed sectors.
Facts About Alcast Company Uncovered
Once you have actually chosen that the light weight aluminum die casting process is ideal for your project, an important following step is choosing the most ideal alloy. The aluminum alloy you select will considerably impact both the spreading procedure and the buildings of the end product. As a result of this, you must make your decision meticulously and take an informed technique.
Determining the most ideal light weight aluminum alloy for your application visit the website will certainly imply weighing a broad array of characteristics. The initial classification addresses alloy attributes that affect the manufacturing procedure.
The Ultimate Guide To Alcast Company
The alloy you choose for die spreading directly influences several facets of the casting procedure, like just how easy the alloy is to function with and if it is susceptible to casting defects. Warm cracking, additionally known as solidification splitting, is a common die spreading defect for light weight aluminum alloys that can result in interior or surface-level rips or cracks.
Specific light weight aluminum alloys are much more at risk to hot splitting than others, and your option ought to consider this. An additional usual problem located in the die spreading of aluminum is die soldering, which is when the cast stays with the die wall surfaces and makes ejection challenging. It can damage both the actors and the die, so you need to search for alloys with high anti-soldering homes.
Deterioration resistance, which is currently a noteworthy quality of light weight aluminum, can differ substantially from alloy to alloy and is an important characteristic to think about relying on the ecological conditions your product will be subjected to (Casting Foundry). Wear resistance is one more residential or commercial property frequently sought in light weight aluminum items and can differentiate some alloys
Report this page